Green Living
Home builders often refer to the exterior of a house as its “envelope” or “shell.” Ensuring that the envelope is sealed against air infiltration (air coming into the house from outside) and air exfiltration (air escaping from inside the house to the outside) can help reduce your energy consumption for heating and cooling the space. Moreover, no one wants to live in a house with drafts.
In this article, we will present different techniques for sealing leaks and improving insulation to create a more comfortable and energy-efficient home. After sealing and insulating the weak points, the work doesn’t end there. We will show you how regular cleaning and water conservation can increase energy efficiency and save you more money on your energy bills. To begin the improvement process, follow these basic sealing guidelines to secure your home’s exterior.
Identifying Leaks
Technicians use a “blower-door test” to accurately measure air leakage in houses. The test involves sealing a portable, frame-mounted fan in an exterior doorway to the house. Any known openings to the outside, such as the fireplace flue; bathroom vent fans; and the flues to the water heater, furnace, or boiler are temporarily sealed.
Once the sealing and setup are complete and the blower fan is turned on, it is possible to measure precisely how much air is entering the house through all the various “unintended” cracks, gaps, and holes in the exterior envelope. Technicians can also identify areas where air is entering the house while the blower door is in operation by using devices called smoke pencils.
While every home is unique and has its own leakage points, there are areas where infiltration consistently shows up in blower-door tests. These areas often include the seam between the top of the foundation wall and the wood framing that runs above, around, and through doors and windows; along baseboards; through electrical receptacles and switches mounted on exterior walls; and around fireplaces, laundry chutes, attic hatchway doors and pull-down stairways, whole-house fan installations, and pipe and wire chases. A homeowner can significantly increase energy efficiency by locating and sealing as many of these entry points as possible.
You don’t necessarily need to have a blower-door test done on your home to locate the unsealed areas that are leaking air. Knowing that these points of air entry have been consistently identified in other houses gives you a starting point for finding gaps and cracks in your home. A windy day outside can also help with this endeavor. Wind can push air into the house through unseen and unnoticed holes to the point that you can feel the air movement.
Examining Exterior Sheathing
Before plywood and oriented strand board (OSB) were invented, homes were built entirely with solid board lumber. The exterior was sheathed underneath the siding with wide boards that, over time, shrank and cracked. All these cracks — and the many others inherent in most homes — are pathways through which air can enter or leave a house. Sidewall sheathing is covered with siding, so all those cracks that appear in and between wide boards on older homes are hidden and inaccessible.
Air can enter a house through various openings in the exterior envelope, such as cracks in the siding, windows, doors, and kitchen or bathroom vents. Even the underside of the lowest course of siding and holes for air-conditioning lines, electrical and gas service wires and pipes can cause air infiltration and exfiltration. Sealing these cracks can reduce air leakage and keep out pests.
Newer homes have fewer seams in the sheathing due to the use of larger plywood and OSB sheets, and installation of house wrap has further reduced air infiltration. Despite this, newer homes still have leakage points that need to be sealed to reduce drafts, energy usage, and keep insects out.
Refrigerant lines passing through the exterior wall of a house create large holes that are often caulked but can develop gaps over time. Closing these gaps with a caulk gun prevents air and insects from infiltrating the house.
Caulking cracks, gaps, and other holes in the exterior “skin” of a house provides both energy savings and building preservation. Minute gaps around doors and windows can let in surprising amounts of air, especially on windy and rainy days. Caulking visible openings on the exterior of a house does not need to wait until it’s time to paint.
In most homes, the wooden framing rests on top of a concrete or concrete block foundation. The lowest section of wood, called the “mud sill,” may not fit securely due to the rough and variable surface of the top of the foundation wall. This gap allows wind to enter the house and should be sealed to prevent air infiltration.
To seal gaps in the exterior envelope of a house, caulk or spray foam can be used depending on which option provides the best access. First, dirt and cobwebs should be brushed away from concrete and wood to ensure that the caulk or foam sticks to both surfaces. The gaps can be filled by aiming the caulk tube’s tip or spray foam applicator tube at them. The job does not have to be neat or precise, as long as it is thorough. In newer homes, a compressible length of foam material is used to fill the gap between the mud sill and the top of the foundation wall. However, it is still worth checking along this area for gaps that may require caulking or foaming. Sealing the interior of the home is also valuable in making it more energy efficient. Gaps between baseboards and hard floors can be filled with latex caulk, while switch and receptacle gaskets made of nonelectrically conductive fiber matt material can be installed to block drafts. It is important to shut off power at the main service panel to avoid electrical shock when removing cover plates from switches and receptacles.
Trouble with Recessed Ceiling Canister Lights
Homeowners face challenges when trying to make their homes more energy-efficient with recessed ceiling canister lights. The older models are not airtight and difficult to seal, which violates fire safety regulations. The solution is to build an airtight box around the light’s housing with flame-resistant materials such as drywall or sheet metal, leaving at least a three-inch gap. However, the box cannot be covered with insulation due to the risk of heat buildup. The heat generated by the light bulbs is usually lost to the attic, which can cause ice dams on the roof during winter. Another alternative is to replace the older models with new, airtight, and energy-efficient “ICAT” canister lights that can be covered with insulation and sealed with caulk for better performance.
The Stack Effect and Attics
The floor of an attic plays a crucial role in energy conservation due to the “stack effect.” Warm air rises and creates pressure at the top of the containment barrier, such as the ceiling of the top floor. Any gap or hole in this area results in pressurized warm air trying to escape, leading to warm air loss and negative pressure inside the house. The incoming cold air needs to be heated, which triggers the furnace or boiler to turn on.
Sealing Fireplace Openings
Sealing an opening around a fireplace can be challenging for builders. The finish wall material, such as drywall or plaster, is supposed to bridge the gap between the wood and the masonry or metal for fire safety and airtight closure. However, gaps around fireplaces can allow air to leave the house easily, which compromises energy efficiency. Comprehensive sealing in this area is crucial to prevent air leakage and save on energy costs.
Inspect your fireplaces by shining a flashlight inside and around them to identify any gaps or holes that need sealing with spray foam, fireproof caulk, or other filler material. This will not only reduce the amount of air escaping through these openings but also protect against sparks or embers jumping out of the fire.
Weatherstripping your doors can help prevent drafts from entering your home and keep your heating and cooling bills in check. In the following section, we will discuss ways to secure your doors better.
Doors can play a significant role in energy efficiency, and while windows usually receive the most attention, doors can make or break your efforts. Doors must open and close smoothly, seal tightly to keep drafts out, and provide insulation to keep the cold at bay.
Various weatherstripping options are available to upgrade your door’s existing weatherstripping. One of the most effective methods is using types containing a vinyl bulb or padded strip set into the edge of a conventional wood doorstop. The flexible wood part is nailed to the doorjamb and seals out air movement, whereas the vinyl bulb or strip does not interfere with the door’s function.
Other weatherstripping types include thin bronze or brass strips nailed inside the jamb where the door closes. The door contacts the metal strip when closing, bending it slightly and ensuring tight contact with the door edge. Though this method is time-consuming, it lasts for years and is an effective draft stopper.
Foam tape is usually not effective as door weatherstripping since it is too bulky and causes the door to bind when applied to the doorstop’s edge. Additionally, it is not durable enough for everyday use.
Some contractors can install vinyl bulb weatherstripping by cutting it into the door frame’s intersection with a special tool resembling a router. A barbed fin on the vinyl bulb weatherstrip is then pressed into the groove, and friction keeps it in place. While effective, it can be challenging to find someone who has the equipment and expertise to install this type of weatherstripping.
Stop Drafts with Door Sweeps and Adjustable Thresholds
When it comes to weatherizing a door, weatherstripping can take care of the top and sides, but the threshold is often overlooked. It’s a difficult area to deal with, as it accumulates dirt and wear over time. Many manufacturers have created solutions to address this problem of drafty thresholds. Some replacement thresholds are complex to install, requiring the removal of the door or cutting off the bottom. Others are easier to install but may not last in harsh weather conditions.
Instead of replacing the entire threshold, consider installing door sweeps or door bottoms. Door bottoms attach to the bottom of the door and can be adjusted to touch the existing threshold as the door closes. Door sweeps attach to the inside of the door near the bottom edge and have a brush or pad that contacts the threshold as the door shuts. Some have a spring-loaded mechanism that clears the door for an entryway mat. Proper installation is essential for these products to be effective.
For particularly difficult doors to seal, installing both a door bottom and a door sweep may be necessary. This way, the second line of defense can stop any draft that gets by the first line.
Adjustable thresholds are found on some doors, but few homeowners make the effort to adjust them over time. It’s a good idea to get down on your hands and knees and look at the area where the threshold is supposed to come into contact with the bottom edge of the door. Often, there will be a wide gap. Adjustable thresholds are typically made from wood or aluminum, and the adjustable part is covered with a removable strip of vinyl. By tightening or loosening the screws, you can adjust the threshold to the proper height.
Older doors with adjustable thresholds may need replacement parts, which can be found at hardware stores, but contacting the original manufacturer is the best option for a perfect match.
Adding storm doors to a home’s entry can provide protection, insulation, and prevent drafts. The effectiveness of the storm door depends on its installation and how well it fits. Aluminum storm doors are screwed onto the door casing, but there may be gaps that can be filled with caulk. The door bottom is another area where air can infiltrate, but most storm doors have an adjustable door bottom that can fit snugly to the threshold. The vinyl strip that seals the storm door bottom to the threshold edge and the weatherstripping on the frame must also be in good condition for the storm door to function correctly. When properly sealed and adjusted, the storm door will make the prime door harder to close, and air will rush out around the sides, top, and bottom. Windows can also contribute to heat and air conditioning loss, especially in older homes with original windows. There are several ways to make windows more energy efficient without spending a lot of time or money.
To seal up cracks between the window and window frame, one option is to use a caulk gun and “weatherstripping caulk sealant” or “temporary” caulking. This type of caulk can be peeled off easily when it’s no longer needed, making it a good choice for those who don’t want to damage paint or clear finishes. However, once the caulk is in place, the window cannot be opened without breaking the seal. Another option is to use lightweight plastic, disposable, interior “storm window systems” which consist of double-stick tape and plastic sheeting that is shrunk with a hair dryer. While these are effective, they may not be suitable for formal areas of the home. In addition to these options, storm windows can also be used to increase insulation and protect prime windows from weather damage. Newer options include permanently installed aluminum or vinyl storms which can be easily adjusted depending on the season. Removing the lightweight screen portion of the storm window during winter can allow for more direct sunlight and solar heating, while also cutting down on noise and keeping out dust and dirt.
To prevent drafts, it’s not enough to just secure windows – it’s equally important to assess the quality of sidewall insulation. This is particularly important for older homes that were built before the invention or perfection of sidewall insulation. As the largest exposure to the outside environment, it makes sense to ensure that sidewalls are as resistant to heat flow as possible. Various materials can be used for sidewall insulation, including cellulose fiber, fiberglass, and different types of foam. Installing insulation from outside the house is the usual protocol, although it can also be installed from inside. However, this job is best left to experts. Attached garages can lead to heat and cooling waste due to “interface” problems, where the garage is not insulated as well as the house. These problems can lead to holes in garage walls, which can compromise fire safety and potentially allow carbon monoxide gas to infiltrate the house.
To prevent air from passing between the house and garage, it is essential to seal up the areas that are susceptible to air leaks. The bottom of the wall inside the garage and the bottom of the doorway into the house are the prime locations that require attention. There is a juncture between the framing and concrete where the bottom of the wall meets the concrete foundation that is similar to the one around the perimeter of the rest of the house. This location lacks a layer of compressible foam between the two materials that would provide an airtight seal. Applying caulk or foam in the garage or inside the basement can effectively seal the gap.
To prevent air from getting drawn into the gap or stud cavities inside the wall, it is worth sealing the bottom edges of the drywall to the concrete using caulk or foam. In negative pressure situations, the air can enter the house through an electrical receptacle in that wall inside the house. Adding gaskets to receptacles on both sides of the wall helps keep contaminated garage air out of the house. Caulking around all the trim and examining the door’s weatherstripping that leads into the house from the garage helps block off this potential air passageway.
In the wintertime, ice dams can form on your roof, causing damage. If you have ice dams forming on your roof, it means that heat is escaping the house and leaking into your attic. Ice dams are the manifestation of energy inefficiency in a home. They are the result of poor air sealing, a lack of insulation, and inadequate ventilation in an attic.
Warm air naturally travels upward, seeking ways to rise even higher through cracks and gaps in the ceiling and walls, causing an accumulation of warm air in the attic. Openings around and through recessed canister lights, whole-house fan installations, attic-access hatchways, pull-down stairs, and electrical boxes in the ceiling and walls all provide conduits from the house into the attic. Additionally, heat is conducted upward through the top-floor ceiling through inadequate attic floor insulation. When snow falls on top of a roof, it acts as insulation, protecting the roof surface from the outside cold air. The combination of heat from below and snow on top creates conditions that warm the roof sheathing and shingles.
When snow lands on a roof, the warm shingles cause the snow to melt. This melted snow runs down the roof until it reaches the edge where it freezes due to the lack of heat. The frozen water then accumulates into ice dams, which can cause significant damage to a home. As the winter progresses, the ice dams grow taller, creating ponds of water behind them. If the water level gets too high, it can seep under the shingles and into the house, causing damage to the interior. The root cause of ice dams is excess heat in the attic, which can be prevented by air sealing and upgrading insulation. This will help to keep the attic cold and reduce or eliminate the formation of ice dams. Proper ventilation in the attic is essential and involves several components such as soffit vents, air channels, chutes, and high roof or ridge vents. It is important to break the thermal bridge created by insulation lying against the underside of the roof sheathing to eliminate the direct conveyance of heat to the sheathing. Adequate attic ventilation also reduces moisture concentration in the attic environment, preventing mildew and mold growth, and can even reduce energy costs in the summer. A comprehensive approach to air sealing, insulation, and ventilation can help prevent the formation of ice dams while also providing benefits in the summer. Tips on how to find and seal weak areas in the attic will be shared in the next section.
Sealing and Insulating Your Attic
Insulation is helpful in preventing heat loss in your attic, but it doesn’t stop airflow. Airflow is a common issue in attics due to cracks, gaps, and holes. These fissures can take many forms, such as holes for wiring, lighting fixtures, and electrical boxes, among others. Every gap represents an opportunity for warm air to escape the rooms below, which means losing energy dollars. Therefore, it’s essential to seal these trouble spots to prevent air leakage.
Sealing most attic floor penetrations is done using caulk and spray foam. Although the application does not have to be neat, it’s crucial to do a thorough job. Any gap left unfilled will leak air. Once you foam or caulk, you can cover the area with insulation again.
Finding and Sealing Leaks
In attics filled with unfaced fiberglass insulation, it’s easy to find spots where air is leaking upward from the rooms below. You’ll often see smudges or staining in the insulation, indicating air leakage. Attics insulated with cellulose fiber don’t show air-leak smudges, so you’ll need to use your sleuthing skills to find areas that likely contain room ceiling/attic floor penetrations. Once you locate a hole that needs filling, use caulk or spray foam to seal it, replace the insulation, and move on to the next spot. Be cautious around wires and electrical boxes and switch off the power before working around them.
When it comes to chimneys, building codes require a two-inch gap between any flammable material and the masonry or metal. This gap is sometimes left unfilled in newer homes, creating a hole that allows warm air to escape through the attic. Older homes may have a smaller gap, but it can still be closed with nonflammable material and fireproof caulk. Sheet metal can be used and sealed with caulk to eliminate any remaining gaps.
Pull-down attic stairways are also a large hole in the attic floor that can allow a lot of air to flow in and out. The undersides of many pull-down attic stair units are made of 1/4-inch plywood that warps away from its sealing surfaces shortly after installation, and the springs that hold the stairway in place lose their resilience over time, creating gaps between the plywood and the jamb. Adding self-stick foam tape along the upper edges of the plywood door can help reduce air leakage, and adding latching devices to the door can cause it to jam tight against the foam weather stripping when not in use. Insulating the door and adding air-sealing capabilities is a more comprehensive solution, and there are kits available such as the “attic tent” or a thick, insulated box that surrounds the stairway opening in the attic. If attic insulation needs to be upgraded, the next section will discuss how to do so.
Improving Attic Insulation
Nowadays, many attics lack sufficient insulation or have insulation that is not functioning at its best. However, upgrading your attic insulation can pay off in the long run and in every season that you live in your home. Adding more insulation to your attic is one of the most effective ways to increase the energy efficiency of your home.
The R-factor is a numerical indication of how well insulation can prevent the flow of heat. The higher the R-number, the better the insulation can stop heat from moving from one place to another. In most parts of the country, the recommended R-factor for attic insulation is R-38. This means you will need around 10 to 12 inches of either fiberglass batting or blown cellulose fiber insulation. However, R-38 is only the minimum recommended standard for attic insulation and proposed energy codes suggest increasing the number to R-50.
Fiberglass batting and cellulose fiber are the two most common attic insulation materials. Both have an R-factor of approximately 3.5 per inch. Cellulose fiber is made from ground-up newspaper material treated with fire-retardant chemicals. Fiberglass is made of glass fibers extruded into batts of specific sizes. Some fiberglass batting is now enclosed in perforated poly bags, making it easier to handle and install. Fiberglass is also available as a loose-fill or blown-in material.
While fitting and installing fiberglass batting around the framing members and obstructions in an attic is possible, it is rare to see a thorough installation. Homeowners and insulation installers often overlook the importance of tightly fitting the material into the many spaces in the attic or find the job too tedious to do it correctly. This leads to gaps and holes between batts and framing, which reduces much of the insulation’s value.
On the other hand, cellulose fiber insulation can be blown into all the nooks and crannies of an attic, allowing it to do a better and more comprehensive insulation job. Nearly any homeowner can do this, and home centers that sell insulation even loan insulation blowers to customers who buy a certain number of bags from their stores. Information on how to operate the machines and install the insulation is available in those stores and from manufacturers.
Cellulose fiber insulation is also less affected by “wind wash” than open fiberglass. Wind wash refers to air currents moving through insulation and robbing it of its R-value. Fiberglass batts enclosed in perforated poly bags are less susceptible to wind wash than open batts or loose-fill fiberglass insulation.
It is possible to install any type of attic insulation over any other type. For instance, you can install fiberglass over cellulose or cellulose over fiberglass with no difference. However, the fiberglass must be unfaced or enclosed in perforated poly bags; otherwise, condensation could develop on the facing.
If you have an attic with a floor that is used for storage, the depth of insulation that can be added is limited by the depth of the floor joists. This means that many attics only have an R-factor of around 20, unless you go to the trouble of removing the floor and adding additional framing lumber to the tops of the joists before reinstalling the floor. However, it is easier to consolidate the stored items into a smaller area or remove them entirely and then roll out poly-encased fiberglass batting on top of the floor. This solution is cheaper and the batts can be removed or rolled back at any time if the space is required for storage in the future.
Attic insulation is a relatively inexpensive way to improve energy efficiency, especially as the price of fuel oil, gas, and electricity continues to rise. However, energy efficiency is not just about sealing and insulating your home. Dust collecting on appliances and irregular maintenance of heating and cooling equipment waste energy. Homeowners who clean and maintain their homes can improve their energy efficiency.
Cleaning and maintenance tasks, such as cleaning the refrigerator coils regularly and replacing the furnace filter, can make a significant difference. The coils underneath and behind a refrigerator are dust magnets, and cleaning them a couple of times a year with a vacuum cleaner and an elongated brush helps the refrigerator operate at its maximum efficiency. Replacing the furnace filter not only improves air quality but also protects the inside of the furnace or air-conditioning evaporator coil. Without the filter, dirt would build up and interfere with the efficient transfer of heat from the furnace or cooling from the air conditioner to the air passing through it.
A furnace filter can impede the flow of air through the furnace, particularly when it becomes dirty. To maintain the furnace’s maximum efficiency, it’s crucial to have a clean filter. Homeowners can replace filters every 30 to 45 days or vacuum them at the same intervals. Pet owners may need to replace or clean their filters more frequently due to pet dander, hair, and dirt brought in from outside. It’s important to remember that in homes with central air conditioning systems, the furnace’s blower distributes cool and dehumidified air during the summer months. Therefore, homeowners should change or clean filters in the summertime at the same frequency as in the winter. The more freely air flows through the furnace, the less energy is wasted, and the more heat and cooling it can distribute.
Heating and cooling equipment, such as furnaces, boilers, and air conditioning systems, have mechanical and electrical components that require lubrication, cleaning, and adjustment over time. The equipment functions best when all parts are working together correctly, as in a tuned-up car. Service people with proper training and equipment should perform the maintenance of HVAC equipment, particularly for newer, more complicated systems. Oil-fired systems should be serviced annually, while gas-fired furnaces and boilers and air conditioning systems should be checked at least every two years. Proper maintenance can improve efficiency, save energy, and extend the life of the components.
Hot water baseboard and electric baseboard heating systems depend on air flowing through the fins surrounding the pipes or heating elements to operate at maximum efficiency. Obstructions due to dirt and dust buildup or something covering the top or bottom of the heating units can compromise the system’s performance. Freely flowing air contributes to better energy efficiency and conservation. Cleaning the fins by vacuuming and brushing them and straightening any bent fins ensures efficient airflow and heat transfer to the air.
Checking Ducts for Air Leaks
It’s important to keep ducts clean to ensure proper airflow of heat and air conditioning to all rooms. Scheduling an annual cleaning service can also help detect any leaks. Shockingly, about 25% of air flowing through poorly installed forced-air duct systems leaks out elsewhere, resulting in wasted energy and money. These leaks can occur in basements, crawl spaces, duct chases, or attics.
The solution to leaky ducts is duct sealing with duct-sealing mastic, which is available in tubs at heating supply houses, hardware stores, and home centers. Duct tape is not suitable for this job as its adhesives break down in the presence of heat. To apply duct mastic, simply smear it around every joint in your ductwork. The mastic has the consistency of pancake batter, and once it cures it stays on the duct without leaking.
Loosely fitting joints and gaps in ducts should also be sealed as soon as possible to improve their performance. After sealing, diverter vanes inside the ducts might need to be adjusted and cleaned to ensure that air is flowing to the correct areas.
Insulating any ducts passing through unheated crawl spaces or attics is also recommended to prevent heat and cooling loss and reduce the workload on the furnace or air conditioner. Duct insulation is available in both wrapping and sleeve types, with sleeves being more effective but requiring temporary disassembly of the ducts.
Maintaining Proper Airflow for Air Conditioners
Air-conditioning systems work by transferring refrigerant from inside the house to outside. The refrigerant absorbs heat from the air passing through the blower compartment of the furnace evaporator coil and is then pumped outside to the condenser coils where heat is extracted from the refrigerant. Therefore, it is important to maintain a clear path for the air conditioner to work effectively.
The air conditioning system’s fan inside the condenser helps in moving air past all the tiny fins and tubes to speed up the transfer of heat from the refrigerant to the outside air. However, this process of cooling air can only happen when the pathways to the compressor are unobstructed. Landscape plantings, decks, ivy, or benches built around and over the compressor can hinder the free flow of air through the system, resulting in a less efficient transfer of heat. Therefore, to make the most of your air conditioning unit, it is advisable to keep the outside compressor unit free of nearby obstructions.
Since the airflow through the condenser is crucial for the efficient functioning of a central air-conditioning system, it is necessary to regularly inspect the outside of the condenser unit. The thin metal fins are delicate and can easily bend if they come in contact with anything such as a baseball, lawn mower tire, or edge of a rake. One can purchase “fin combs” inexpensively from heating supply stores or home centers, which can straighten several rows of bent fins at once.
Apart from cleaning and minor maintenance, there are other steps one can take around the house to improve energy efficiency. In the next section, we will discuss strategies for effective water conservation.
Water Conservation
Enhancing water conservation in one’s home can help save not only on water bills but also on expenses for heating water. Below are some ideas to try to boost water conservation efforts.
Removing Sediment Buildup
Draining sediment from a water heater’s tank is an energy-saving procedure that anyone can quickly and easily do. Periodically removing accumulated sediment helps conventional water heaters operate at optimal efficiency. The sediment comprises of hard-water minerals and other debris that enter the storage tank with the incoming water. As the water heats up, the minerals separate from the water and settle at the bottom of the tank.
Over time, the mineral deposits accumulate to the point where they act as insulation on the bottom of the tank, isolating the water from the effects of the burner firing below (on gas and oil units) and sometimes stacking up high enough to cover the heating element on electric water heaters. The harder it is for heat to pass through the sediment layer, the longer the burner has to fire or the electric elements have to run to heat the water.
The solution is to remove the sediment layer. One does not need to turn off the power source (electricity, gas, or oil) to the water to drain the sediment.
A small drain valve is located on the outside of the water heater tank’s jacket near the bottom. It looks like a miniature hose bibb on the outside of a house. Connect a short length of standard garden hose to this valve, stick the free end of the hose into either a nearby floor drain or a large bucket, and open the valve.
Water will flow from the bottom of the water heater and out the valve and through the hose, taking sediment along with it. After draining around five gallons from the tank, shut off the valve, disconnect the hose, and empty the bucket (if you used one) into a sink or toilet. This not only improves the efficiency of the water heater but also extends its service life.
The reason for the popping, banging, rumbling, and percolating noises often heard from a water heater is due to the accumulated sediment and a thin film of water that is trapped between the sediment and the bottom of the tank. When the burner fires, the thin layer of water heats up to an abnormally high temperature, which deteriorates the tank’s glass lining and speeds up the rusting process. To prevent this, a water heater tank should be drained of its sediment at least twice a year, and more often in hard-water areas.
Pipe insulation keeps heat inside the pipes where it belongs, reducing the volume of water that has to flow down the pipe for hot water to effectively arrive. This results in hot water reaching distant bathrooms faster than it would otherwise. Additionally, pipe insulation reduces “standby” heat losses at the water heater by preventing heat from radiating out into the air. Insulating the first five feet or so of the cold water pipe at the water heater helps reduce the loss of heat that migrates up the pipe from the water heater tank. Insulating the pipes at the water heater can add up to substantial savings over the course of a year.
It may also be worthwhile to insulate the water service entry pipe from a municipal supply or well to prevent condensation from forming on the outside of the pipe during winter and into the spring. Insulating water pipes these days is simpler, quicker, and more effective than it used to be.
The closed cell foam pipe insulation, which can be found at plumbing supply stores and home centers, not only provides better insulation than the old fiberglass material, but it’s also simple to install. Each piece is designed to snap over the pipe, as it’s been slit down its length. The foam itself is soft enough that you can use a kitchen knife or heavy scissors to cut it.
Adding an Insulation Blanket to Your Water Heater
Today, new water heaters are built with better insulation, so if you have an old unit, consider adding an extra layer of insulation to it. You can purchase water heater “blankets” from home centers and hardware stores, which will wrap the exterior of the water heater with an additional layer of insulation.
You can cover electric water heaters from top to bottom with insulation. However, gas water heaters should not be covered on top or along the bottom. The top has a flue, which can get hot enough to ignite flammable materials. As for the bottom, it must be left open so that air can enter the burner assembly, which is necessary for the proper combustion of natural gas, propane, or oil.
You must also leave the end of the pressure and temperature relief valve extension pipe open and exposed, which usually runs down the side of the water heater. This pipe must be free of obstructions in case the valve activates and releases hot water or steam. Any blockages could interfere with the release of pressure within the tank and can be dangerous.
Aside from these precautions, the more insulation you can wrap around your water heater, the fewer “standby” losses you’ll have. This means that the burner or elements will come on less often, making it more efficient overall. Though this task is not glamorous, it’s easy and inexpensive, offering a payoff every hour of every day once you add the insulation blanket.
Installing Low-Flow Showerheads
Almost half of all household water usage is from bathing, and almost all of that water must be heated. Thus, the bathroom is an ideal place to conserve both energy and water. Since January of 1995, new homes have been required to have showerheads that dispense no more than 2.5 gallons per minute. If you have an older showerhead, replacing it with a showerhead that meets current flow rate standards will take only a few minutes.
Showerheads are not expensive. For ten to twenty-five dollars, you can purchase a new showerhead that adheres to the 2.5-gallon limit. If you replace an older showerhead that allows up to 6 gallons per minute with a low-flow showerhead, you’ll save more than three gallons per minute while showering.
In northern states, water entering homes in the winter can be as cold as 38 degrees. Heating water that cold to the 120 degrees needed for a reasonably hot shower requires quite a bit of energy. Therefore, taking advantage of 2.5-gallon showerhead technology can lead to significant savings on your utility bill.
One important thing to note is that using a low-flow showerhead does not mean you can spend more time in the shower. Sometimes, the length of your shower is limited by how much hot water your water heater can hold. If your old showerhead used up all the hot water in ten minutes, and your new low-flow showerhead uses six gallons per minute, technically you could take a 20-minute shower, but you wouldn’t save any energy or water. To really save energy and water, keep your shower routine the same and only use the water you need for washing, rinsing, and getting out.
For older-style sink faucets, they can deliver 3.5 to 5 gallons of water per minute, which is often more than what’s needed for typical washing tasks. Faucet aerators are a great solution, either as a retrofit add-on or supplied with new faucets. They reduce the flow rate to 0.5 to 1.0 gallon per minute in bathrooms, and 1.0 to 2.0 gallons per minute in the kitchen. Air is added to the water stream to make it feel fuller, while using less hot water.
Remember, heat and air conditioning can escape from your home through leaks, poor insulation, and appliances or equipment that aren’t properly cared for. By following the guidelines in this article, homeowners can take control and minimize these weak areas.
©Publications International, Ltd.
FAQ
1. What are some easy ways to make my home more energy efficient?
Some easy ways to make your home more energy efficient include installing programmable thermostats, sealing air leaks around windows and doors, and replacing old light bulbs with energy-efficient LED bulbs.
2. How can I reduce my energy usage during the summer months?
You can reduce your energy usage during the summer months by keeping your blinds and curtains closed during the day to block out the sun’s heat, using a ceiling fan instead of air conditioning when possible, and planting trees or shrubs around your home to provide shade.
3. What are some energy-efficient heating options for my home?
Some energy-efficient heating options for your home include geothermal systems, high-efficiency furnaces, and pellet stoves.
4. How can I make my appliances more energy efficient?
You can make your appliances more energy efficient by choosing models with an Energy Star label, using your dishwasher and washing machine only when they’re full, and cleaning your refrigerator coils regularly.
5. What are some energy-efficient lighting options?
Some energy-efficient lighting options include LED bulbs, compact fluorescent bulbs, and halogen incandescent bulbs.
6. How can I save energy while doing laundry?
You can save energy while doing laundry by washing your clothes in cold water and air-drying them instead of using a dryer.
7. How can I reduce my water usage and make it more energy efficient?
You can reduce your water usage and make it more energy efficient by fixing leaks promptly, installing low-flow showerheads and faucets, and using a dishwasher instead of washing dishes by hand.
8. What are some ways to make my windows more energy efficient?
Some ways to make your windows more energy efficient include installing weatherstripping around the frames, using double-paned windows, and adding window film.
9. How can I make my home more energy efficient on a budget?
You can make your home more energy efficient on a budget by sealing air leaks with caulk or weatherstripping, using a programmable thermostat, and using LED light bulbs.
10. How can I determine my home’s energy usage?
You can determine your home’s energy usage by checking your utility bills and using an online energy calculator.
11. What are some ways to make my home more energy efficient during the winter?
Some ways to make your home more energy efficient during the winter include adding insulation to your walls and attic, using a humidifier to make the air feel warmer, and using a fireplace insert or wood stove instead of a traditional fireplace.
12. How can I make my home more energy efficient if I rent?
If you rent your home, you can make it more energy efficient by using door sweeps to prevent drafts, using a window insulation kit, and using energy-efficient light bulbs.
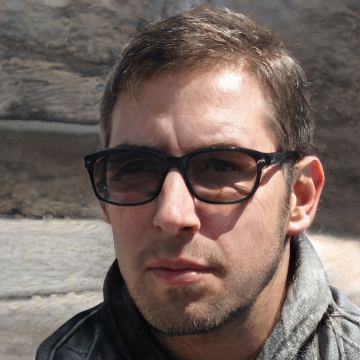
Brody is a skilled craftsman and gardening expert. From renovating living spaces to cultivating lush gardens, Brody’s knowledge and passion shine through, inspiring readers to embark on their own home improvement and gardening journeys with confidence.
Leave a Reply